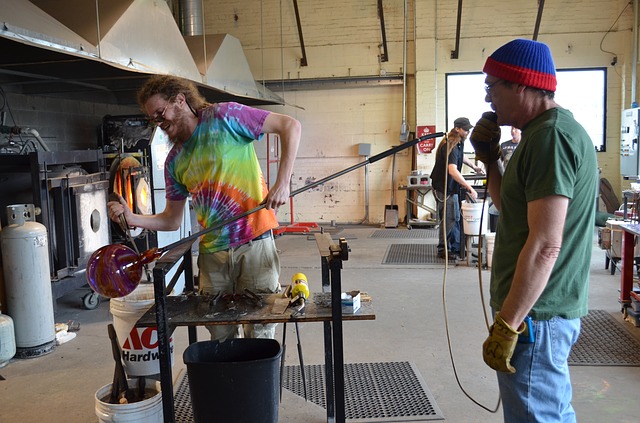
Extraction to Melting – Glass Making Process Explained
Glass has become so common place that it is now easy to see directly through it without hesitation. It may be found in our windows, screens, closets, and many of the electrical devices we use every day.
Even though glass can be seen almost everywhere, you may waste your entire life without understanding how it is made or what it is formed of. Even if you think you know the basics, you’ve just scratched the surface. So, if you want to know how are glass bottles made or how ordinary glass is made, this article is for you. So, let’s get started.
Table of Content
What is Glass?
Glass is a translucent, solid-like material used in a wide range of standard applications. Glass is created by combining tangible and plentiful essential elements (such as sand, soda ash, and limestone) at incredibly high temperatures to create a new material: glass.
At high temperatures, glass behaves like a liquid, yet it acts like a solid at room temperature.
As a result, the glass may be poured, blown, crushed, and molded into a wide variety of shapes.
Glassmaking has a lengthy history, dating back to around 3500 BC in Egypt and Mesopotamia when it was first artificially made for use as jewellery and subsequently as vessels. Since then, methods have advanced from handcrafting to today’s high-tech industrial procedures, and the range of glass types and applications has exploded.
Consider Bohemian crystal, Italy’s Murano Island, the Palace of Versailles’ Mirror Gallery, or cathedral stained glass. Glass is all about us these days, and it continues to deliver cutting-edge solutions for high-tech applications, either alone or in combination with other materials; this trend is sure to continue in the future.
Is Glass Made of Sand?
Minerals such as silica sand, soda ash, limestone, magnesium oxide, and aluminium oxide are commonly used to make a glass bottle. Other materials like zinc, fluorides, iron, copper, and so on may be seen if you look closely at a coloured glass container. However, because a glass container typically contains 70 to 74% silica by weight, the main component remains sand.
Turning sand (and other materials) into glass requires a lot of heat and skill. For centuries, skilled artisans blew the glass and shaped it into a helpful bottle or rolled it into beautiful sheets of glass for church and cathedral windows. Today’s glass is made with high-precision machinery to create bottles and jars with tight tolerances and consistent quality.
How Is Glass Made?
The glass business is characterised by various production procedures that differ depending on the finished product and its intended use. All of these manufacturing processes, on the other hand, have one thing in common: glass must first be melted!
Glass melting needs the use of two different types of raw materials: sand and recycled glass. To manufacture molten glass, these basic materials are mixed, placed into a furnace, and melted at around 1500°C. The molten glass is then taken out of the furnace and formed before being cooled.
The resulting glass can be further processed to have specific properties for various applications, such as increased mechanical strength and breaking resistance.
The specific composition of glass varies depending on the use.
Still, soda-lime glass, the most often used form, is made up of silica sand, soda ash, limestone, dolomite, and glass cullets (recycled glass). Extra elements such as iron oxide or cobalt can be added to the mix to give the glass a green or blue touch.
Methods of Glass Making
Molten glass gobs are sliced with a carefully timed blade before entering the forming machine to ensure that each gob is of comparable weight. Each glass container’s forming process is dependent on the importance of a gob.
The bottle’s neck and basic shape are made by gravity pushing gobs of melted glass into a forming tool, where pressure forms the bottle’s neck and bare body. Once the neck finish and overall glass bottle shape are complete, the form is known as a parison. To achieve the final container shape, one of two procedures is used.
Press and Blow Method
While manufacturing glass bottles, the Press and Blow method is the most often used method; it makes numerous containers of the same size at the same time using an individual section (IS) machine that is divided into variable portions. The molten glass is chopped into specific gob sizes using a shearing blade.
The gob falls into the device due to gravity. A metal plunger is used to push the gob into the mould, where it begins to solidify and become a parison. After that, the parison is placed in the blow mould and warmed until it is malleable enough to complete the glass measurements.
After the parison has been warmed to blowing temperature, the air is introduced to create the container. Because their size allows the plunger to fit the parison, press and blow procedures are commonly utilised to develop broad bottles and jars.
Blow and Blow Methods
The Blow and Blow technique is used to create thin containers. It also demands the employment of an IS machine to feed molten glass into the mould by gravity. The parison’s neck finish and basic bottle form are created with compressed air.
After that, the parison is reheated and twisted 180 degrees before being blown into its final shape with air. Once again, compressed air is utilised to blast the container into the proper form. Glass bottles with variable neck thicknesses are best produced using the Blow and Blow procedures.
Finishing the Process
After the bottle has been made, it is removed from the mould and carried to the annealing lehr, regardless of the process used. The bottles are reheated to roughly 1,050 degrees in the lehr before being gently cooled to around 390 degrees.
This process allows the glass to cool steadily, eliminating internal tensions that may lead to cracking or shattering. After that, the bottles are thoroughly tested to verify that they meet quality control criteria.
Wrapping Up
So, this was how glass is made from their extraction from the sand like silica to melt and shape them. Thus, after going through the article, if it has been clear to you how glass is made, then you may also start manufacturing it. However, first, you should begin to have less quantity and with time, your business’s size.