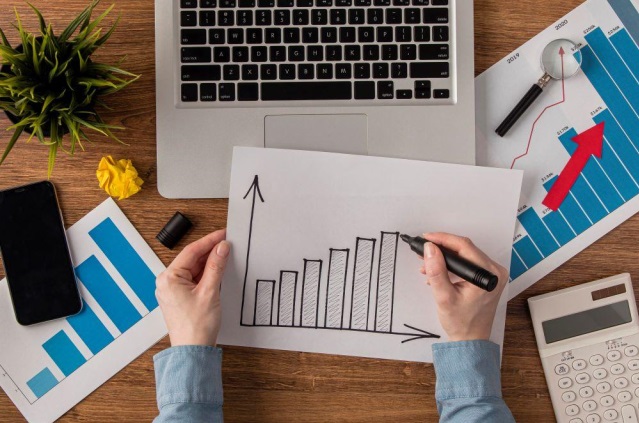
What Is Six Sigma? A Deep Dive into This Methodology
In this article, we will strive to provide you with all the information you may need to fully understand what is Six Sigma and how it can help you transform and grow your business in the fastest way possible.
Table of Content
- 1 Deciphering the Basics – What is Six Sigma and How Does it Work?
- 2 Statistical Analysis vs. Guesswork Is the Core Distinction in Understanding What Is Six Sigma
- 3 Key Concepts Demystified – How to Navigate the DMAIC Framework of Six Sigma
- 4 Data-Driven Decision Making Is the Heart of Six Sigma Implementation
- 5 Tools and Techniques in Six Sigma – Common Practices for Effective Implementation
- 6 Measuring Success with Key Performance Indicators (KPIs)
Deciphering the Basics – What is Six Sigma and How Does it Work?
Before anything else, you must know what is Six Sigma. It’s essential to understand this methodology and how it will transform your business. Its core principle is using statistical precision to improve different factors and parameters of your business. The final goal is the growth of your business.
The first type of improvement that you can expect from this method is a reduction in the process defects of your business. Six Sigma is able to reduce the errors to as low as 3.4 per million, which is as close to perfection as possible. To achieve this, a massive focus is put on the decisional process used by your company. It’s vital to always use a data-driven approach to achieve this incredible result.
To make the method as easy to understand and implement as possible, a framework was created to systemize every part as much as possible. Using DMAIC (define, measure, analyze, improve, and control), any process of your business can be easily enhanced and brought to the highest levels of effectiveness and efficiency.
Statistical Analysis vs. Guesswork Is the Core Distinction in Understanding What Is Six Sigma
The core principle you must learn if you want to understand what is Six Sigma and implement it flawlessly is statistical analysis. Unfortunately, even today, many businesses use goalscoring. They base many of their decisions on intuition and subjective judgments instead of doing thorough research and analysis. If your company manages to change its approach when it comes to making decisions, it will be much easier to find the roots of any problems, which will allow you to create the ideal solutions.
Just imagine how much your business can be improved if all the current processes are fully optimized. Its growth in the next few years will be phenomenal, and you can reach all your goals many times faster. On the other hand, you will need the help of professionals and be willing to make all the changes required.
If you want to implement this method correctly, it’s essential to understand the DMAIC framework. Without it, it will be impossible to reach the highest possible levels of optimization. For this reason, you must start by having a basic understanding of each of the Define, Measure, Analyze, Improve, and Control steps.
Every time Six Sigma is used for any type of project, the first part is to define all the requirements, be they for your business or those of your customers. The goals must also be included to have a guiding light toward the finish line. Next, it’s time to measure every factor and parameter that influences the goals and the results of the process. Having as much data as possible is essential for the following steps.
After all the information and data is collected, it must be analyzed to find all the errors and problems that must be corrected. This takes us to the next step, where the process will be improved by first solving all the defects found. Professionals will develop all the solutions required to maximize the effectiveness and efficiency of your process. Finally, the last step ensures you have maximum control to guarantee the longevity of all the changes made.
Data-Driven Decision Making Is the Heart of Six Sigma Implementation
As you can see from the basics explained above, the core of Six Sigma remains data-driven decision-making. Overall, this method introduces the scientific methodology to the business sector, adapting it to ensure maximum effectiveness.
The main advantage of using this method is the elimination of subjective judgments, which are known to fail frequently. When the process has a high degree of complexity, it’s impossible to make realistic judgments without using a data-driven approach. For this reason, Six Sigma will make massive improvements to any businesses that are still basing all decision-making processes on guesswork or intuition.
Tools and Techniques in Six Sigma – Common Practices for Effective Implementation
Even with all the steps of the Six Sigma process explained you must know that their implementation is not so simple. There is a complete set of tools that are to be used for different purposes. So, you will need a professional who is adept at using all the instruments to ensure the proper implementation of this method.
To give you a few examples, a Control Chart will be used for monitoring purposes, Pareto Analysis will gather information about the defects and their contributors, and the Fishbone Diagram or Ishikawa Diagram will be used to detect the root cause of the problems discovered.
There are also tools used for the analysis and decision-making steps, such as Regression Analysis and Hypothesis Testing. All these tools and more are another core part of Six Sigma and what makes it so effective and essential for any business.
Measuring Success with Key Performance Indicators (KPIs)
KPIs are another reason why Six Sigma manages to maximize the effectiveness and efficiency of any process. Instead of leaving the interpretation of the results to a subjective judgment, the key performance indicators are used to ensure a realistic and quantifiable result is reached.
To give you a few examples of KPIs that are used in the Six Sigma method, you can find DPMO (defects per million opportunities), cycle times, customer satisfaction, and overall process efficiency and the main ones.
Using these KPIs, your team will always know exactly what improvements were made, what the results are, and how much you can expect to improve your company in the future. You can also use them as a guiding light that will show you the correct future direction for your business.